
同軸コネクタ、1個から最短即日出荷可能です。
製品の紹介・購入、在庫確認、各種資料請求など、製品についてなんでもお問い合わせください。
目次
- 同軸コネクタ開発の流れ|仕様検討から検証まで
- コネクタ開発の第一歩:仕様を決める
- 設計図から製品へ:コネクタ設計の舞台裏
- 職人の技と設備でつくる:製造工程とは
- 開発完了へ:検証・テストの内容
- よくある質問(FAQ)
PDF資料はこちら
同軸コネクタ開発の流れ|仕様検討から検証まで
同軸コネクタが出来るまでに、以下の4ステップを踏みます。
ステップ① | 仕様検討 |
ステップ② | 設計 |
ステップ③ | 製造 |
ステップ④ | 検証 |
コネクタ開発の第一歩:仕様を決める
使用周波数帯を始めとした、様々な仕様を机上で検討します。ここで決めた仕様で「設計」を行い、その内容を「検証」します。
適合ケーブル
電気的特性:使用周波数帯、絶縁抵抗、耐電圧、接触抵抗、など
機械的特性:互換性、ケーブル引張強度、結合部接続強度、など
対候性:防水性、浸食性、など
設計図から製品へ:コネクタ設計の舞台裏
「仕様検討」で決めた仕様を満たすために、同軸コネクタの材質・構造・表面処理・寸法などを「設計」をします。
組立方法検討までする場合や、設計データを元に「電磁界シミュレーション」を行い、電気的特性精度を「製造」前に確認する場合もあります。
材質の種類
同軸コネクタ本体に使用される材質を設計します。それぞ特長があるため、仕様に応じて使い分けます。
名称 | 特長 |
真鍮(黄銅) | 銅と亜鉛の合金で、弊社の同軸コネクタでは最も多く使われています。 柔らかくて加工性が良い材質です。 |
ステンレス鋼 | 鉄を主成分とし、炭素1.2%以下、クロム10.5%以上を含んだ合金鋼です。英語では「Stain(サビ)+ less(にくい)」。鉄より錆びにく、耐熱性・強度は真鍮(黄銅)に勝りますが、コスト面と加工性は、真鍮の方が優位となります。 |
亜鉛ダイカスト | 溶かした非鉄金属を金型に流し込んで成形する鋳型方式をダイカストと呼び、その金属に亜鉛合金を用いたものを亜鉛ダイカストと言います。流動性が高く、薄く複雑な形状の製品を高い精度で製造出来ます。 |
ベリリウム銅 | 銅をベースに0.5~3%のベリリウムを加えた合金です。強度と耐久性・耐熱性・耐食性に優れています。特に極めてバネ性が優れており、トーコネでは中心コンタクトに使用されることが多く、コネクタ本体では真鍮(黄銅)と一緒に使われることが多いです。 |
リン青銅 | 銅とスズの合金である青銅に、りんを加えることで、青銅内部に含まれる酸化銅を脱酸した金属です。バネ特性に優れ、耐食性・耐疲労性があり、耐摩耗性に優れます。 |
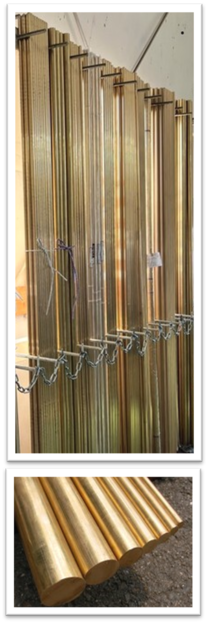
真鍮(黄銅) 棒
表面めっきの種類
金属または非金属の材料表面に金属の薄膜を被覆することです。めっきの手法として、電気的な力で被めっき物の表面に処理を行なう「電気(電解)メッキ」と、化学薬品の力で同様の処理を行なう「無電解メッキ」が、同軸コネクタに対しては一般的です。材質と同じく、仕様に応じて使い分けます。
名称 | 特長 |
ニッケルめっき(Ni) | 耐食性に優れ、表面処理の他に下地メッキとしても使用されます。 |
金めっき(Au) | 電気・熱の伝導性、耐食性に優れています。 |
銀めっき(Ag) | 電気の伝導性やはんだ付け性、相互変調の低減に優れています。空気中で酸化、微量の硫化物で黒変し易い性質があるのが注意点。 |
三元めっき(CnSnZn) | 銅(Cn)・亜鉛(Zn)・すず(Sn)を合わせた三元合金。他のメッキ処理と比べて相互変調の低減に優れています。 |
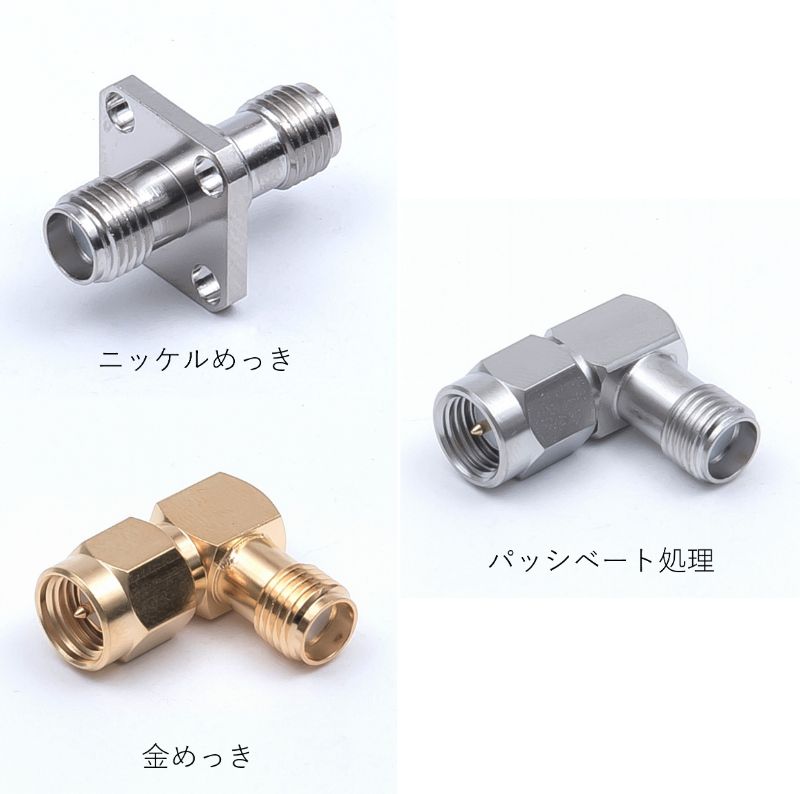
豆知識:パッシベート処理(Pa)
ステンレスは、もともと表面が酸化皮膜により覆われており、錆びにくい素材と言われています。ただ、この皮膜は非常に薄く、何らかの要因で傷つくことがあり、そこから錆が発生します。そこで、この皮膜を厚くして防錆性能を向上させるため、硝酸系の酸化剤で処理を行うことをパッシベート:不動態化と言います。寸法変化の少ない優れた表面処理です。
トーコネのステンレス製同軸コネクタでも、めっき処理ではなく、パッシベート処理を施してます。
職人の技と設備でつくる:製造工程とは
「設計」で決めたことに従って、同軸コネクタの「製造」を行います。
トーコネの同軸コネクタの多くは、真鍮(黄銅)の切削加工によって製作されています。
切削
トーコネの同軸コネクタの多くは、NC旋盤による切削加工で、真鍮(黄銅)を削り出しています。
より細かい寸法が求められる場合などには、マシニングセンターによるマシニング加工がおこなわれます。
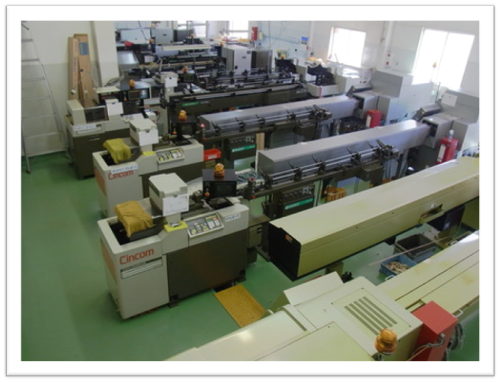
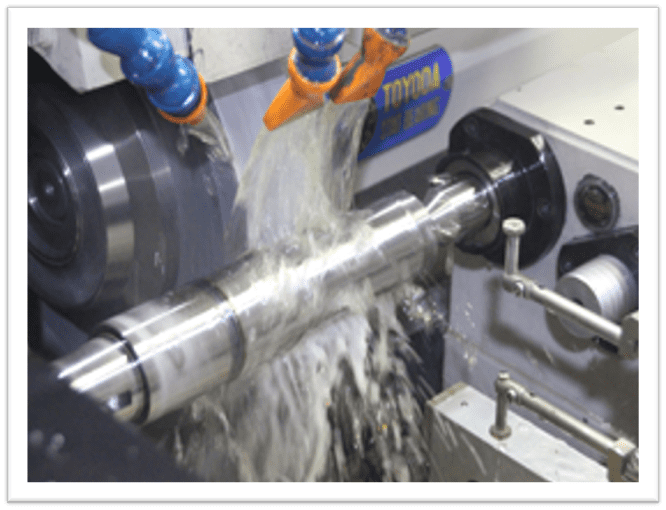
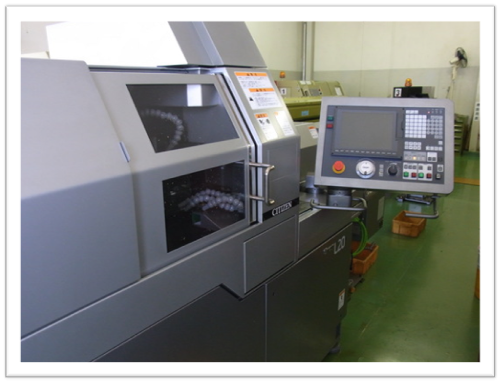
NC旋盤による切削加工(4倍速)
豆知識:ダイカスト
金型鋳造方法のひとつで、ダイキャストとも呼ばれます。金型に溶融した非鉄金属を圧入することで、短時間に大量生産する方式です。
金型製作のための初期コストがかかってしまうため、弊社では切削を選択することが多いですが、Lotや寸法によっては、ダイカストで製作します。
例:BNC-BRダイカスト
研磨
切削後の部材は、バレル研磨を用いて、バリなどを取ります。
バレル研磨は、部材と研磨石と一緒に回転させることにより、摩擦で部材のバリなどを取る装置です。
表面めっき処理
研磨した部材は、組み立て前にめっき処理を施します。めっきの種類は前述した通りです。
組み立て
表面めっき処理を終えた部材は、他の部材と組み立てます。組み立てには様々な工具と治具を用い、作業者による差異が出ないような工夫が施されています。
組み立て例①
組み立て例②
組み立て例③
開発完了へ:検証・テストの内容
「製造」された同軸コネクタが、「設計」した仕様を満たしているかを確認する、「検証」を行います。
確認が必要な仕様によって、様々な検証方法があります。
通常検証
・ ネットワークアナライザ測定試験(V.S.W.R、リターンロス、挿入損失等)
・ 絶縁抵抗試験
・ 耐電圧試験
・ 接触抵抗試験
・ ケーブル引張強度試験
・ 結合部接続強度試験
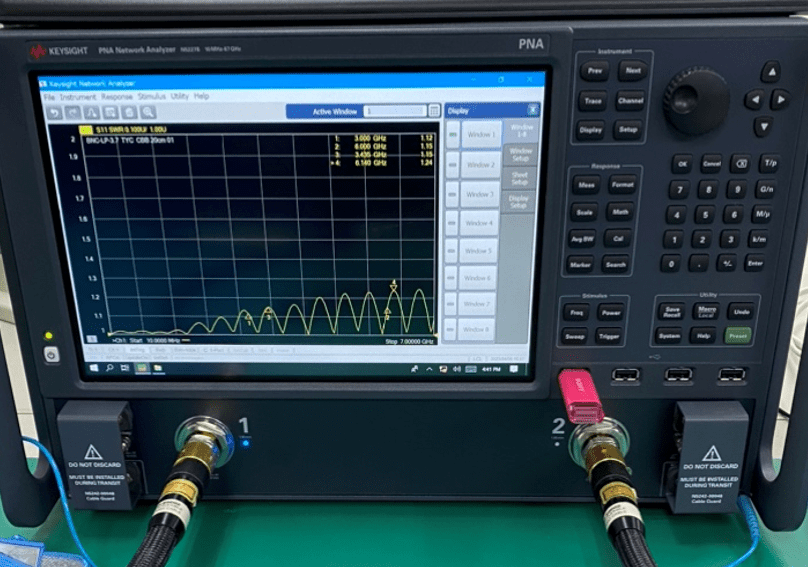
ネットワーク アナライザー
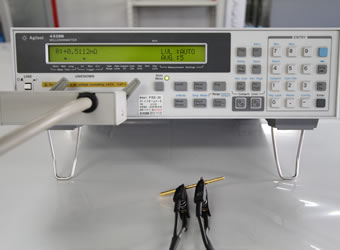
1kHz mΩメーター器
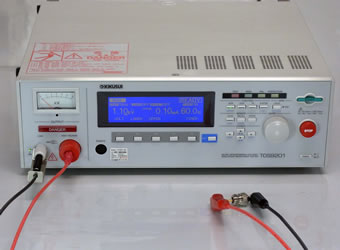
耐電圧・絶縁抵抗試験器
特別検証
外部施設等も活用し、コネクタ仕様に合わせて様々な検証を行うことが可能です。
・ 耐熱試験
・ 耐寒試験
・ 熱衝撃試験(温度サイクル)
・ 耐食性試験
・ 耐腐食性試験
・ 耐衝撃試験
・ 耐振動性試験
・ 耐水性試験(IP☓7)※IP☓5も簡易的に実施可能
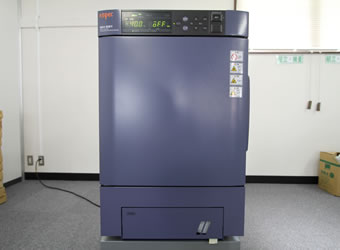
恒温恒湿試験器
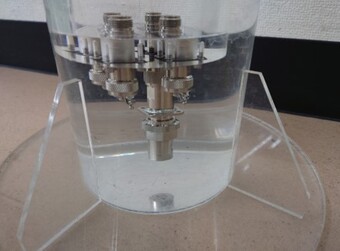
防水性試験(IP☓7)
その他、環境・品質関連トピック
よくある質問(FAQ)
Q
同軸コネクタの開発にはどれくらいの期間がかかりますか?
A
製品の仕様や要求レベルによりますが、標準品ベースのカスタムであれば1〜2ヶ月、新規開発品の場合は3〜6ヶ月程度が一般的です。
Q
仕様検討ではどのような点を決めるのですか?
A
使用周波数、インピーダンス、嵌合相手、環境条件(温度・湿度・耐振動など)を基に、構造や材料の方向性を定めます。
Q
設計ではどんなツールや技術が使われますか?
A
CADによる3D設計、電気的特性シミュレーション(Sパラメータなど)、構造強度解析などが活用されます。
Q
製造は国内ですか?
A
当社はファブレスメーカーです。設計までを自社で行い、製造工程は協力会社にておこなっております。そのため、製品に応じて、国内・海外両方での製造を使い分けております。